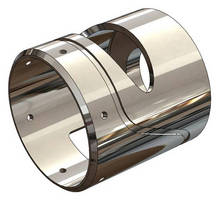
Delcam has launched the 2014 release of its Delcam for SolidWorks integrated CAM system, the first version to include the Vortex strategy for area clearance. The software also includes a number of new options for turning, four-axis rotary machining and turn-mill operations, plus more strategies for two-axis finishing.
Full details on the new release and videos of the new functionality are on www.delcam.tv/dfs2014/lz.
Vortex, for which Delcam has a patent pending, has been developed specifically to gain the most efficient material removal from solid carbide tooling, in particular those designs that can give deeper cuts by using the full flute length as the cutting surface. It can be used for two- and three-axis roughing, three-plus-two-axis area clearance and for rest machining based on stock models or reference toolpaths.
Unlike other high-speed roughing techniques that aim to maintain a constant theoretical metal-removal rate, the Vortex strategy produces toolpaths with a controlled engagement angle for the complete operation. This maintains the optimum cutting conditions for the entire toolpath that would normally be possible only for the straight-line moves. As a result, the cutting time will be shorter, while cutting will be undertaken at a more consistent volume-removal rate and feed rate, so protecting the machine.
Because Vortex toolpaths have a controlled engagement angle, tools should never be overloaded and so will achieve the maximum tool life. Shock loading caused by changes in the contact angle is minimised, preventing chipping of the flutes. In addition, the stability of the cutting conditions gives more consistent edge temperatures, so prolonging the life of the tool coating and removing heat damage to the surface of the part. Finally, the ability to use stepdowns of up to two, or even three times, the tool diameter spreads the tool wear evenly over the cutting surface of the tool, again contributing to longer tool life.
The first improvement to turning in Delcam for SolidWorks 2014 gives the ability to add fillets to any sharp corners, for example, for automatic deburring, without having to edit the geometry. The user simply has to specify the radius to be applied and all the sharp corners will be filleted automatically.
Turning simulation has been made more realistic with the ability to program and simulate the movements of the steady-rest that can be used to position large parts during turning and the tailstock that can be used to hold long parts on centre during machining. Collision detection against both these types of accessory is undertaken automatically during both cutting and transfer operations.
Improved support for machines with four-axis rotary tables allows two- or three-axis operations to be wrapped around the rotary axis. The same option also supports wrapped features for turn-mill operation. The wrapped feature can be taken directly from the SolidWorks model using the feature-from-feature concept at the heart of Delcam for SolidWorks.
Toolpath editing has been added for all strategies. This allows segments within the toolpath to be deleted or to be divided into smaller segments. Segments can also be connected.
A number of extra strategies and options have been added for two-axis finishing. These include dedicated strategies for finishing the bottoms of pockets and continuous spiral machining either from outside to inside or inside to outside.
More efficient machining has been made possible with the ability to clip both roughing and finishing passes to stock models. This reduces air moves that might otherwise be generated when machining arbitrary shapes, such as castings or forgings.
Finally, programming in Delcam for SolidWorks has been made safer with a new option to identify certain surfaces as check surfaces to be avoided. This is particularly useful to avoid collisions with clamps and other accessories. |